The full extent and scale of the damage is still unknown.
Experts Adnan Seric and Deborah Winkler predict that as a result of coronavirus, we will see a surge in automation, whilst subsequently seeing globalisation diminish.
The current COVID-19 pandemic has fully exposed the vulnerabilities of global value chains (GVCs) which are characterised by high interdependencies between global lead firms and suppliers located across several continents. Many countries are currently facing supply shortages of critical medical equipment, in particular from China, which has also been labelled ‘supply-side contagion’ (Baldwin and Tomiura 2020). Firms and nations are also facing risks associated with protectionist national trade policies: high import tariffs may have caused shortages of critical medical products and equipment from China in the US (Bown 2020), while export restrictions on medical supplies may have exacerbated supply shortages (Evenett et al. 2020).
Long before the COVID-19 pandemic, in an effort to mitigate supply chain risks, increase flexibility, and improve product standards, global lead firms have relied on Industry 4.0 technologies, such as robots, 3D printing, and smart factories, and occasionally reshored parts of their production. Even in developing countries like Bangladesh, for instance, contract manufacturers in the apparel industry have started replacing workers with robots to adapt to increasing wages (Wall Street Journal 2018). Confronting this pandemic could accelerate some of the trends of the past few years including technology adoption and the use of new data (Goldberg 2020). In view of those pertinent changes, this column aims to examine the following policy relevant question: could the current crisis further spur automation and reshoring in GVCs?
Global demand for ventilators and personal protective equipment (PPE), such as medical masks, plastic shields, and gloves has increased exponentially as the number of COVID-19 cases has skyrocketed. Countries are consequently facing supply shortages of critical medical equipment and parts and components of such equipment and are looking to Industry 4.0, including 3D printing and artificial intelligence, to fill some of these supply shortages. The US Food and Drug Administration, for instance, is collaborating with government and public-private partners, including America Makes, the National Additive Manufacturing Innovation Institute, to respond to the shortages in medical supplies using 3D printing to produce ventilator valves and other ventilator parts, as well as face masks and plastic shields (Force Biotech 2020).
From a lead firm perspective, Industry 4.0 unlocks new labour-saving technologies which could potentially reduce reliance on low-skill, low-cost labour in manufacturing. This has implications for the global geography of production, as value chains can be expected to become more regional in nature, moving closer to key final consumer markets (in China, the EU, Japan and the US). Industry 4.0 is also likely to have an impact on the length of value chains, as automation could consolidate various steps of the value chain. And Industry 4.0 could influence the reshoring decisions of lead firms in light of the growing importance of supportive and flexible business ecosystems (Hallward-Driemeier and Nayyar 2017). A firm-level survey involving a sample of around 2,500 manufacturing firms from eight European countries confirms that flexibility and product quality were the two main drivers for their reshoring activities in 2015 (Figure 1).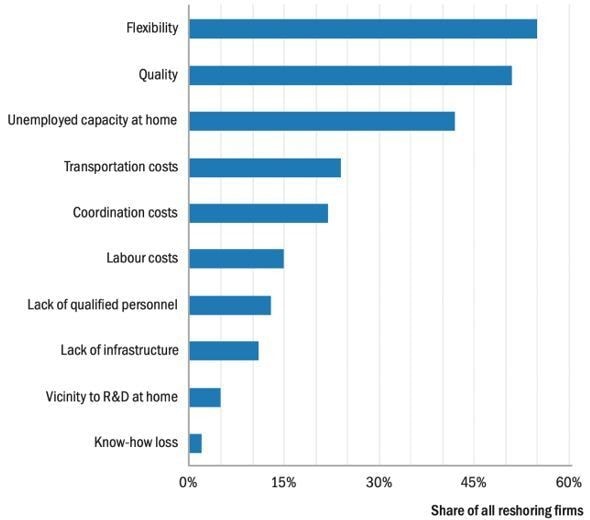
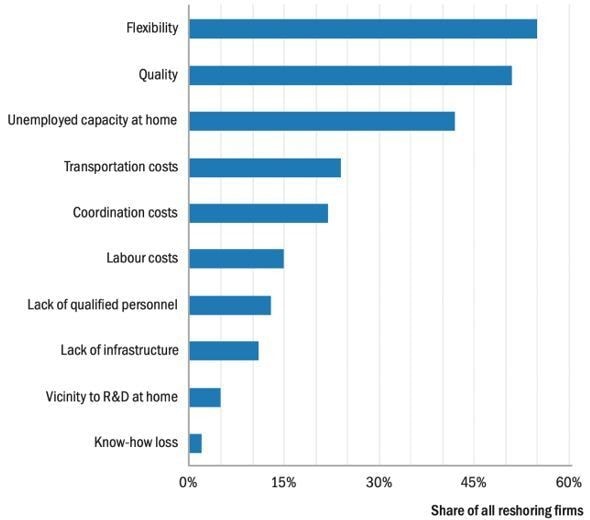
Figure 1 Flexibility and product quality were the main reasons for reshoring.
Image: Dachs and Seric (2019) and UNIDO (2019), based on the European Manufacturing Survey 2015
Several factors seem to support the argument that automation and possibly reshoring will accelerate following the COVID-19 pandemic. Automation and reshoring allow for more flexible adjustment to changing demand, mitigating firms’ risks in the event of a pandemic or other shock. The case of automatic testing for COVID-19 in the Republic of Korea – i.e. samples are analysed by a diagnostic machine rather than by humans – exemplifies that automation facilitates supply-side adjustments (e.g. through on-demand ordering), speeds up the testing process, and reduces risk of error and contamination (CNN 2020). Industrial policies that aim to strengthen a country’s healthcare sector and reduce its dependence on global supply chains could accelerate the trends towards automation and reshoring, particularly involving goods deemed critical to national security. This possibility has recently been voiced by politicians and economic advisers in the US and elsewhere (The Hill 2020).
There are also, however, reasons to be unconcerned about a full reversal of globalisation
Ensuring the supply of critical goods does not necessarily require reshoring of production. Countries can prepare for a pandemic by stockpiling ventilators and critical medical equipment, even if these have been produced abroad, as well as by implementing health sector reforms that have been long overdue. While firms may rethink their strategies and consider automation or reshoring to mitigate future risks, it is unlikely that entire supply chains will be automated in the short term. The automation of certain sub-components may not be feasible or even desirable, for example, due to a shortage of skilled workers who are able to operate the machines or for products with low value-to-weight ratios.
The global stock of industrial robots is still concentrated in specific countries and manufacturing industries (Figure 2). As of 2016, around one million industrial robots in the manufacturing sector were being used in countries specialised in innovative GVC tasks. These countries are characterised by high GVC participation, a high share of manufacturing and business services in their exports, and a high engagement in innovation, and include many European countries, Canada, the US, Israel, and some Asian countries (Japan, Singapore, and the Republic of Korea) (World Bank 2019). While China alone used over 260,000 robots in its manufacturing production, the other countries used only 150,000 robots. Nearly half of the robots were used in motor vehicle production (664,000), followed by computers and electronics (close to 400,000). Robots were used to a lesser extent to produce rubber and plastics, fabricated metals, machinery and equipment, and food and beverages.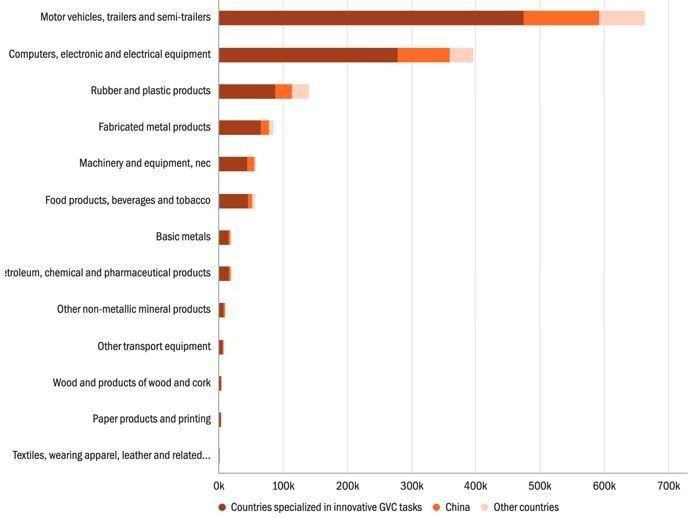
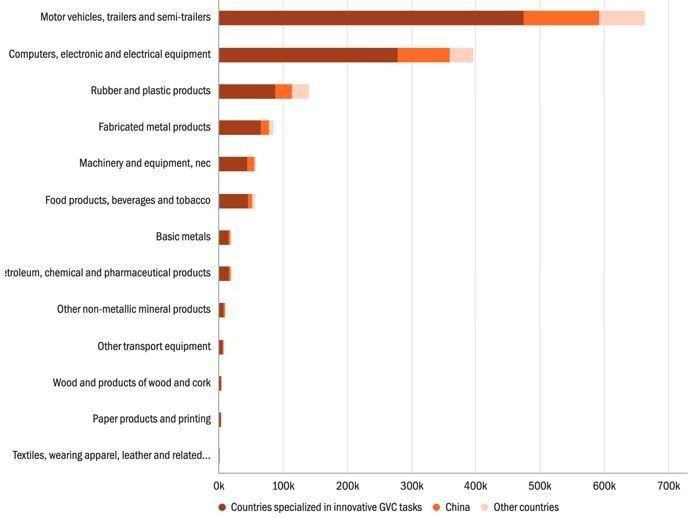
Figure 2 Industrial robots are still concentrated in specific countries and industries.
Image: International Federation of Robotics
Furthermore, the data do not unanimously support a negative association between automation and GVC participation. Although backward GVC participation in the manufacturing sector fell in most countries between 2011 and 2016, while the industrial robot stock increased, their relationship varies by type of country. The scatterplots present the correlation of countries specialised in innovative GVC tasks compared to China and other countries (Figure 3a + 3b). While the analysis does not reveal any causality, the differences between country types are striking. Higher robotisation in countries specialised in innovative GVC tasks (top panel)—which use the bulk of industrial robots—appears to be associated with a weaker decline in GVC participation. A recent study finds that robotisation in industrialised countries has promoted South-North trade of parts and components across various industries between 1995 and 2015 (Artuc et al. 2018). The scatterplot for China and other countries (bottom panel), by contrast, shows a negative correlation. Higher robot use is associated with a stronger decline in backward GVC participation. The implications for development depend on types of foreign inputs sourced from a given country (labour-intensive or not) as well as on the relationship between robots and labour in the relevant industries.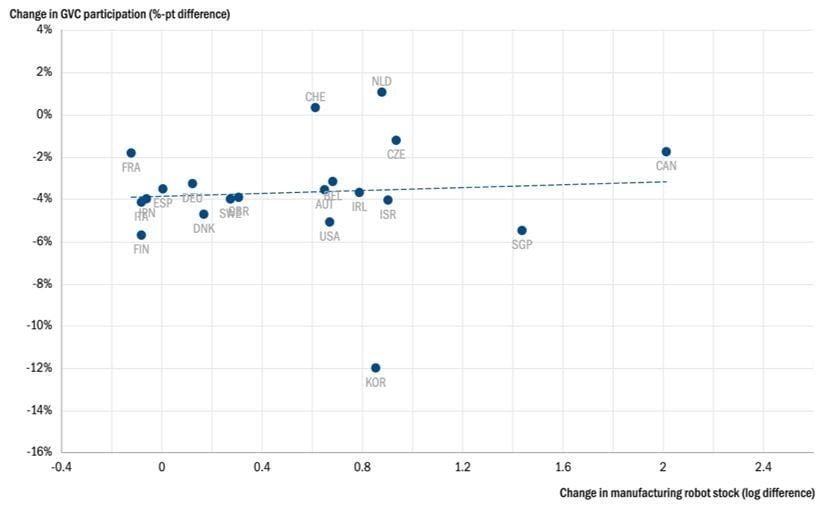
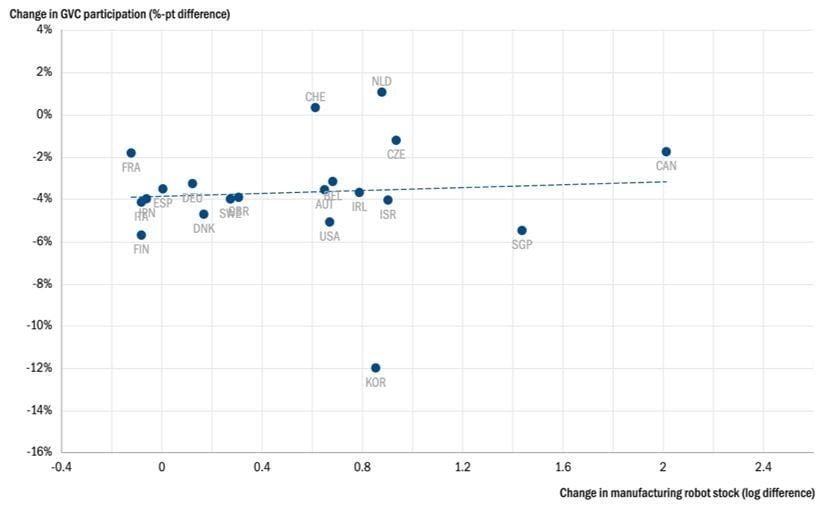
Figure 3a Relationship between automation and GVC participation in manufacturing varies
Figure 3b Relationship between automation and GVC participation in manufacturing varies
Image: International Federation of Robotics and OECD TiVA
Other developments—including GVC entry of lower-cost countries and growing demand for mid-range consumer goods in emerging markets—could actually slow down the trend towards automation and reshoring. Ethiopia, for instance, has successfully entered GVCs and created many jobs for apparel workers, especially women, but currently has no regulated minimum wage, making the country an attractive investment location for global apparel lead firms (Africanews 2019). Moreover, appetite for inexpensive consumer products like electronics and apparel is growing in emerging markets. Original equipment manufacturers such as Tecno (Hong Kong Special Administrative Region), Torque (the Philippines), and Viettel (Viet Nam), for example, have been penetrating the smart phone markets in Asia and Africa (Perlman 2017). Automation and reshoring seem to be less likely in labour-intensive GVCs that target consumers in emerging markets, at least in the short to medium-term.
The coronavirus pandemic has already taught us several lessons. From a trade perspective, free flows of crucial goods and services ranging from masks and ventilator components exported from China to doctors being flown in to Italy from Cuba (Reuters 2020), the automation of critical tasks such as testing, and the absence of trade protectionism and red tape all jointly play a role in overcoming this pandemic and to improve preparedness. These lessons will hopefully be remembered when we shape the post-COVID-19 world.
Editor’s note
Originally published on 22 April 2020 by UNIDO’s Industrial Analytics Platform (IAP), a digital knowledge platform that combines expert analysis, data visualizations and story telling on topics of relevance to industrial development. The views expressed in this column are those of the authors and do not necessarily reflect the views of UNIDO or other organizations that the authors are affiliated with.
No comments:
Post a Comment